Streszczenie
Artykuł poświęcono zagadnieniu technologiczności tradycyjnego sposobu odlewania dzwonów. Pomimo złamania podstawowych zasad poprawnego projektowania technologii odlewania, tradycyjna technologia wykonywania dzwonów sprawdza się od setek lat. Autorzy analizując wyniki badań brązu CuSn20-C oraz tradycyjnej masy formierskiej używanej do wykonywania form na dzwony, próbują wykazać na czym polega tajemnica fenomenu najstarszej z aktualnie stosowanych technologii odlewania.
Wstęp
Gdyby poprosić sto przypadkowych osób o wymienienie wytworów sztuki odlewniczej o najdłuższych tradycjach, zdecydowana większość na pierwszych trzech miejscach wymieniłaby, obok pomników i armat, dzwony. Jeśli się głębiej nad tym zastanowić to właśnie dzwony najbardziej zasługują na miano „tradycyjnych” odlewów. Jest to chyba jedyny typ odlewów, który do dziś wykonywany jest z wykorzystaniem materiałów i technik stosowanych od setek lat.
„Dźwięczny” brąz na dzwony to zanany od wielu wieków dwuskładnikowy stop miedzi i cyny o zawartości od 18 do 22% Cu. Już u schyłku jedenastego wieku mnich Teofil podaje zalecenie dotyczące składu brązu na dzwony: „Aby dzwon miał odpowiedni dźwięk miedź i cyna powinny zostać zmieszane przed odlewaniem. Cyna powinna stanowić jedną piątą lub jedną szóstą”[1]. W późniejszych opracowaniach można napotkać następujące informacje dotyczące składu brązu na dzwony „..do metalu na dzwony bierzemy trzy części miedzi i jedną część cyny (z niewielkim dodatkiem srebra lub bizmutu)”[2].
Pomimo tego że wśród stopów miedzi ujętych w normie PN-EN 1982-2002 nie znalazł się, obok innych dwuskładnikowych stopów miedzi i cyny, stop o zawartości 20% cyny, do dzisiaj, dzwony wykonuje się właśnie z takiego brązu. Mimo prób zastąpienia rzadkiej, a co się z tym wiąże kosztownej cyny innymi pierwiastkami nie udało się uzyskać stopu o podobnych właściwościach „dźwiękowych”[3].
Ze stopu CuSn20-C, bo takie oznaczenie nosiłby wg normy PN-EN, odlewa się także pierścienie tłokowe, łożyska, tuleje itp. W przeciwieństwie do normy europejskiej brąz ten ujęty został w normach ASTM (B22) i UNS (C91300).
Podobnie długą tradycją cieszy się także masa formierska, z której wykonuje się formy na dzwony. Podstawowym składnikiem tej masy jest glina, do której w zależności od regionu, być może zależne jest to od właściwości lokalnej gliny, dodaje się różnych materiałów. Dodatkami takimi są między innymi: sieczka słomiana, trociny, konopie i koński nawóz. Proporcje składników różnią się znacząco w zależności od przeznaczenia masy, czy jest to rdzeń, płaszcz, forma korony czy wreszcie fałszywy dzwon (rys. 1).
O ile brąz CuSn20-C pod względem struktury, właściwości fizycznych i mechanicznych oraz użytkowych jest znany, a informacje te można znaleźć w literaturze. To informacje o właściwościach tradycyjnych mas formierskich stosowanych na formy na dzwony są bardzo skąpe i trudno dostępne. Pracochłonność wykonania formy dzwonu z tradycyjnej masy i tradycyjną techniką skłania ludwisarnie do poszukiwania innych materiałów formierskich, które pozwoliłyby na uproszczenie technologii, skrócenie czasu przygotowania formy i obniżenie kosztów. Niektóre z europejskich odlewni dzwonów, ©Royal Eijsbouts czy ©GRASSMAYR stosują masy chemoutwardzalne na osnowie z piasku
kwarcowego ale pociąga to za sobą konieczność wykonania odpowiedniego oprzyrządowania dla każdego wymiaru dzwonu i problem z utylizacją zużytej masy. Koszty takiej modernizacji są bardzo duże i małe rodzinne ludwisarnie nie mogą sobie na to pozwolić. Dlatego do dzisiejszego dnia, w niektórych rejonach Europy, jeszcze możemy zobaczyć proces wykonywania dzwonu niezmieniony od setek lat.
Technologia wykonywania formy dzwonu jest zasadniczo bardzo prosta, do tego stopnia, że udało się ją przedstawić na jednej fotografii (przy pomocy jednego eksponatu muzealnego, rys. 1.). W skrócie, polega na wymurowaniu podstawy rdzenia, następnie nałożeniu na niego warstwy masy glinianej i nadanie jej kształtu wnętrza dzwonu przy pomocy obrotowego wzornika. Na wysuszony rdzeń nakładana jest warstwa masy, której nadaje się zewnętrzny kształt dzwonu także przy pomocy odpowiedniego wzornika. Po wysuszeniu tworzy ona tzw. fałszywy dzwon. Na powierzchni fałszywego dzwonu, po uprzednim jej przygotowaniu umieszcza się wszelkie zdobienia, napisy czy płaskorzeźby wykonane z wosku. Na tak „ubraną” formę nakłada się warstwami, każda warstwa jest indywidualnie suszona, masę formierską tworząc w ten sposób tzw. Płaszcz, czyli górną część formy. Po jej wysuszeniu płaszcz ściąga się i usuwa fałszywydzwon, w ten sposób po ponownym złożeniu rdzenia i płaszcza wewnątrz uzyskuje się pustą przestrzeń w kształcie klosza dzwonu. Po złożeniu i dodaniu formy korony, która wykonywana jest metodą traconego wosku, oraz zabezpieczeniu formy przed rozszczelnieniem zasypuje się ją ziemią w dole odlewniczym. Metal doprowadza się do formy jednym lub kilkoma, w zależności od wielkości dzwonu, otworami w koronie przy pomoc odpowiednio ukształtowanej rynny, w formie korony wykonuje się także otwory odgazowujące (rys. 2).
Jak wynika z powyższego opisu i zdjęcia formy przedstawionego na rysunku 1, dzwon odlewany jest w pozycji „naturalnej”, w takiej w jakiej będzie zawieszony. Zatem część klosza o najgrubszej ściance, miejsce w które uderza serce, znajduje się najniżej w formie. Ta część ma także największą średnicę co skutkuje tym, że środek ciężkości dzwonu znajduje się na około 1/3 jego wysokości, wliczając koronę. Wynika z tego że połowa masy krzepnącego w formie metalu znajduje się poniżej jednej trzeciej wysokości wnęki formy, a część o najgrubszej ściance oddalona jest o ponad 0,9 wysokości wnęki formy od miejsca zasilania, „nadlewem” zaś jest fragment rynny połączony z otworem wlewowym. Należy jeszcze dodać że, podczas „pracy” dzwonu, najbardziej obciążona mechanicznie jest pozioma ścianka łącząca klosz z koroną.
Od wielu stuleci jest więc praktykowana technologia odlewania, której wszystkie elementy zaprojektowano wbrew zasadzie krzepnięcia kierunkowego. Dlaczego zatem dzwony „wychodzą” i dlaczego codziennie z wież kościelnych, od małych wiosek po wielkie miasta, na całym świecie słychać ich dźwięk?
Materiały i badania
Brąz CuSn20-C
Badany stop został wytopiony z czystych składników: miedzi o czystości 99.99% i cyny o takiej samej czystości w proporcji 4:1. Stop podczas wytopu nie został poddany żadnym zabiegom metalurgicznym, a powierzchnia kąpieli zabezpieczona została przed wpływem atmosfery jedynie węglem drzewnym. Po przegrzaniu stopu do temperatury 1100 st. C odlano próbki do dalszych badań oraz wykonano odlewy prób technologicznych, o których będzie mowa w dalszej części pracy.
Struktura otrzymanego brązu CuSn20-C składa się z plastycznej miękkiej fazy alfa oraz mieszaniny eutektoidalnej fazy alfa i twardego związku międzymetalicznego delta (Cu31Sn8) (rys. 3), który odpowiada za jego akustyczne właściwości [3-5]. Ponadto w stanie lanym w strukturze brązu w całej objętości badanych próbek występują charakterystyczne drobne międzydendrytyczne pustki (rys. 4).
Chociaż zgodnie z układem równowagi fazowej Cu – Sn w temperaturze otoczenia stop miedzi o dwudziestoprocentowym dodatku cyny powinien mieć strukturę składającą się z fazy alfa i epsilon (rys. 5). W warunkach krzepnięcia w formie odlewniczej, ze względu na małą dyfuzję miedzi nie zachodzi przemiana delta -> alfa + epsilon. Potwierdza to analiza termiczno-derywacyjna (ATD), na krzywej krystalizacji nie występują żadne lokalne ekstrema w pobliżu temperatury 350 st. C (rys. 6). Dlatego analizując strukturę i proces krystalizacji brązu CuSn20-C krzepnącego w formie odlewniczej powinno się korzystać raczej z układu metastabilnego (rys. 7) [6].
Pod względem metalograficznym stop ten zdaje się być standardowym dwuskładnikowym stopem odlewniczym.
Jakimi zatem własnościami odlewniczymi on się charakteryzuje?
Ocenie poddano skłonność do tworzenia jam skurczowych, wykonano w tym celu standardową próbę technologiczną polegającą na odlaniu sześciennego odlewu testowego. Wyznaczono także wartość skurczu odlewniczego swobodnego i hamowanego wykonując odlewy próbne, w formie z masy utwardzanej CO2 oraz w formie wykonanej z tradycyjnej masy na bazie gliny (rys. 8).
Obliczone wartości liniowego skurczu niehamowanego i hamowanego wyniosły dla formy CO2 odpowiednio: 1,51 i 1,03%. Dla formy z masy glinianej wartość skurczu zarówno hamowanego jak i niehamowanego wyniosła 0.
Na rysunku 9, dla porównania, przedstawione zostały zdjęcia przekroju odlewu technologicznej próby do oceny skłonności do tworzenia jam skurczowych brązu CuSn20-C oraz żeliwa sferoidalnego GJS 500-7.
Masa formierska HS
Badaną masą była tradycyjna masa stosowana do wykonywania form dzwonów w Pracowni Ludwisarskiej Jana Felczyńskiego w Przemyślu. Składnikami masy są lokalnie pozyskiwana glina oraz nawóz koński, stąd dalej masa będzie nazywana masą HS. Masa została dostarczona z ludwisarni w stanie gotowym do użytku.
Z masy wykonane zostały standardowe próbki przeznaczone do badań wytrzymałości na rozciąganie i ściskanie (rys. 10) na uniwersalnym aparacie wytrzymałościowym typu LRu.
Po wykonaniu, próbki były suszone w temperaturze 180 st. C przez 1h, a po wysuszeniu, w celu określenia wpływu temperatury wyżarzania na własności masy, po trzy próbki z każdego rodzaju wygrzewano w temperaturach 200, 250, 300, 350, 400 i 500 st. C w czasie 30 minut. Tak przygotowane próbki badano na aparacie LRu wyznaczając wytrzymałość na rozciąganie. W przypadku próby ściskania zakres pomiarowy aparatu LRu okazał się niewystarczający dlatego próby statycznego ściskania przeprowadzono na uniwersalnej maszynie wytrzymałościowej WPM – VEB LEIPZIG.
Wyniki badań w postaci diagramów zmian wytrzymałości na rozciąganie i ściskane w zależności od temperatury wyżarzania przedstawione zostały na rysunkach 11 i 12. Wykresy uzupełniono o krzywe procentowego ubytku masy próbek, w stosunku do masy po wstępnym suszeniu, w zależności od temperatury wyżarzania.
Rezultat technologicznej próby oceny wartości skurczu odlewniczego z użyciem formy wykonanej z masy HS, był dużą niespodzianką. Dlatego przeprowadzono dodatkowe badania przy użyciu automatycznego dylatometru DA-2, wyznaczając krzywe procentowej zmiany długości próbek w funkcji temperatury. Badaniom, w identycznym cyklu nagrzewania i chłodzenia, poddano próbki brązu i masy HS. Uzyskane wyniki w postaci krzywych procentowej zmiany długości próbek w funkcji temperatury przedstawione zostały na rysunku 13.
Analiza wyników i podsumowanie
„Mikroporowatość występuje szczególnie w stopach o dużym zakresie temperatur krystalizacji, gdzie skurcz początkowy jest częściowo skompensowany przez ruch mieszaniny ciekło-stałej. W miarę postepowania procesu krzepnięcia dendryty tworzą koherentną sieć zakrzepłego tworzywa i przepływ cieczy szczątkowej zachodzi wtedy poprzez kanały między dendrytyczne. Jeżeli w stanie ciekłym metal zawiera dostateczną ilość rozpuszczonych gazów, ich atomy przenikają do porów skurczowych i podwyższają ciśnienie na skutek zmniejszenia rozpuszczalności gazów w metalu z obniżeniem temperatury. Przepływ metalu do porów międzyziarnowych zostaje zatrzymany w chwili, gdy przestrzenie ziarnowe zostaną zamknięte.” Ten fragment podręcznika autorstwa prof. J. Braszczyńskiego [7], podręcznika, który znany jest wszystkim odlewnikom w Polsce najlepiej wyjaśnia pochodzenie mikro porów zaobserwowanych w strukturze badanego stopu CuSn20-C. Tworzenie się ich w trakcie krystalizacji w całej objętości odlewu skutkuje brakiem występowania skupionej jamy skurczowej w węzłach cieplnych (rys. 9). Oznacz to, że cała różnica w objętości fazy ciekłej i stałej brązu występuje w postaci milionów drobnych porów rozsianych równomiernie w całej objętości metalu. Dlatego w odlewach dzwonów, mimo braku zasilania, nie występują skupione jamy skurczowe.
Jak wynika z opisu mechanizmu tworzenia się mikroporowatości, wg J. Braszczyńskiego niezwykle istotną rolę pełnią w nim gazy rozpuszczone w ciekłym metalu. Jeśli rozpuszczonych gazów będzie zbyt mało ciśnienie w tworzących się porach będzie zbyt niskie i nie zahamuje mikrozasilania kanałami międzydendrytycznymi. W takiej sytuacji metal będzie wykazywał tendencję do tworzenia pustek o większej objętości skupionych w pobliżu osi ścianki odlewu (porowatość osiowa). Jeśli ilość rozpuszczonych gazów w metalu będzie zbyt duża to duża ilość atomów gazów przenikająca do tworzących się porów spowoduje nadmierny wzrost ciśnienia i zwiększenia objętości porów a co za tym idzie obniżenie gęstości metalu w stanie stałym.
W obu przypadkach, porowatości osiowej czy gazowej, skutkiem jest brak odpowiedniego dźwięku dzwonu. Dźwięk jest zbyt niski, w przypadku porowatości gazowej i niskiej gęstości lub brakuje właściwego zgrania tonacyjnego pomiędzy dźwiękami składającymi na głos dzwonu w przypadku rzadzizny osiowej.
Cała finezja i kunszt ludwisarzy w przygotowaniu stopu polega na tym aby metal przegrzać i przetrzymać w takiej temperaturze aby umożliwić rozpuszczenie gazów, a następnie przeprowadzając odgazowanie kontrolować ilość gazów pozostających w kąpieli metalowej. Dodatkowy podziw wzbudza to że, w tradycyjnym procesie odbywa się to w piecu szybowym opalanym koksem, a do „odgazowania” zaś służy świeżo ścięty konar drzewa liściastego.
Specyfika krzepnięcia, odpowiednio przygotowanego, brązu CuSn20-C pozwala na otrzymywanie zdrowych odlewów dzwonów bez stosowania żadnych układów zasilających. Ale jak niemal każdy stop odlewniczy w stanie stałym, tak i brąz na dzwony zmniejsza swoją objętość wraz ze spadkiem temperatury.
Jak wynika z badań dylatometrycznych (rys. 13) brąz CuSn20-C charakteryzuje się stosunkowo dużym skurczem w stanie stałym bo wynoszącym ponad 2,5% w przedziale temperatury 100 – 775 st. C. Biorąc pod uwag kształt dzwonu, wymuszający tworzenie się naprężeń rozciągających podczas kurczenia się odlewu i „zgniatania” rdzenia oraz wysoką wytrzymałość na ściskanie masy, z której wykonany jest rdzeń 0,5-0,7 [MPa]. Wartość naprężeń wywołanych hamowaniem skurczu powinna doprowadzić do pękania odlewów jeszcze w formie lub podczas uderzenia serca.
Dlaczego dzwony nie pękają, a jeśli pękają to nie jest to skutek naprężeń odlewniczych. Częściowo odpowiedź kryje się w wynikach technologicznej próby określania skurczu liniowego wykonanej w formie z masy HS. Odpowiedź dopełnia porównanie fragmentów krzywych dylatometrycznych brązu CuSn20-C i masy HS, zarejestrowane dla etapu chłodzenia cyklu pomiarowego (rys. 14). Widać że masa HS i brąz kurczą się niemal identycznie od temperatury 775 st. C do 450 st. C (przebieg krzywych niemal równoległy). Poniżej 450 st. C masa HS kurczy się w znacznie mniejszym stopniu w porównaniu do brązu niemniej jednak finalna różnica to niespełna 1%.
Rozgrzany pod wpływem ciepła ciekłego metalu rdzeń zwiększa swoje wymiary, a następnie po zakrzepnięciu odlewu kurczy się wraz z nim nie hamując zmiany wymiarów dzwonu a tym samym nie wywołując w kloszu dzwonu naprężeń. Ponadto w wysokich temperaturach dodatki organiczne znajdujące się w masie ulegają wypaleniu, przez co masa staje się porowata i znacząco spadają jej właściwości mechaniczne. Rozwiązaniem okazuje się odpowiedni dobór składników masy i ich proporcji oraz wygrzanie formy w odpowiedniej temperaturze, takiej która pozwala uzyskać odpowiednie właściwości mechaniczne formy i całkowicie pozbyć się wilgoci z masy (rys. 11 i 12).
Podziękowania
Autorzy pragną złożyć serdeczne podziękowania Pracowni Ludwisarskiej Jana Felczyńskiego z Przemyśla za udostępnienie materiałów do badań, przekazanie wielu cennych informacji oraz za życzliwość i pomoc w realizacji badań.
Literatura
[1] Theophilus, (1963). Manuscript. Notes on Various Arts, in: VTs NILKR Reports, Issue 7.
[2] Denisov F. (1828). Detailed Guide to General Technology, Tipogr. Semena Selivanovskogo, Moscow.
[3] Lisovskii V. A., Lisovskaya O. B., Kochetkova L. P. & Favstov Yu. K. (2007). Sparingly Alloyed Bell Bronzes with Elevated Parameters of Mechanical Properties. Metal Science and Heat Treatment Vol. 49, No. 5 – 6.
[4] Saunders N., Miodownik A.P. (1990). The Cu-Sn (Copper-Tin) System, Bulletin of Alloy Phase Diagram Vol. 11 No. 3.
[5] Favstov Yu. K., Zhuravel L. V., & Kochetkova L. P. (2003). Structure and Damping Capacity of Br022 Bell Bronze. Metal Science and Heat Treatment Vol. 45, No. 11 – 12.
[6] Kondracki M. (2013). Stopy miedzi. In Sobczak J.J (Eds.), Poradnik Odlewnika. Tom 1 Materiały (pp. 521-545). Kraków, Wyd. STOP.
[7] Braszczyński J. (1989). Teoria procesów odlewniczych. PWN Warszawa.
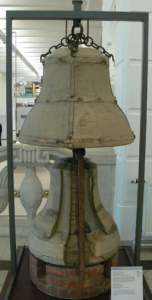
Rys. 1. „TMW – Glockenguss” by Wolfgang Sauber, forma odlewnicza dzwonu jako eksponat w Wiedeńskim Muzeum Techniki
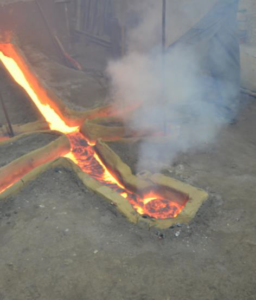
Rys. 2. Zalewanie formy-„narodziny dzwonu”, widoczne gazy wydobywające się z formy przez otwory w formie korony (fot. Pracownia Ludwisarska Jan Felczyński, http://www.janfelczynski.com/)
- Rys. 3. Podstawowe składniki struktury brązu CuSn20-C w stanie lanym (x500)
- Rys. 4. Struktura brązu CuSn20-C w stanie lanym z widocznymi pustkami między dendrytami fazy alfa (x50)
- Rys. 5. Układ równowagi fazowej Cu-Sn [6]
- Rys. 6. Wykres ATD brązu CuSn20-C
- Rys. 7. Metastabilny układ Cu-Sn; linia przerywana – odlew krzepnący w formie piaskowej, linia kropkowana – odlew krzepnący w formie metalowej [6]
- Rys. 7. Metastabilny układ Cu-Sn; linia przerywana – odlew krzepnący w formie piaskowej, linia kropkowana – odlew krzepnący w formie metalowej
- Rys. 9. Przekroje odlewów technologicznej próby oceny skłonności do tworzenia jam skurczowych
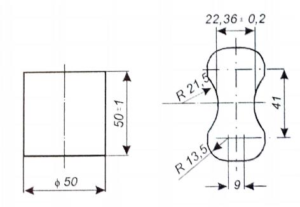
Rys. 10. Geometria standardowych próbek stosowanych do badania właściwości mas formierskich
- Rys. 11. Wytrzymałość na ściskanie masy HS w zależności od temperatury wyżarzania
- Rys. 12. Wytrzymałość na rozciąganie masy HS w zależności od temperatury wyżarzania
- Rys. 13. Krzywe dylatometryczne brązu CuSn20-C i masy HS wraz z krzywą cyklu zmian temperatury w czasie
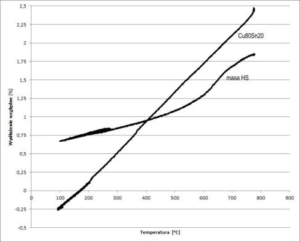
Rys. 14. Fragmenty krzywych dylatometrycznych brązu CuSn20-C i masy HS, zarejestrowane dla etapu chłodzenia cyklu pomiarowego
Nowe komentarze